
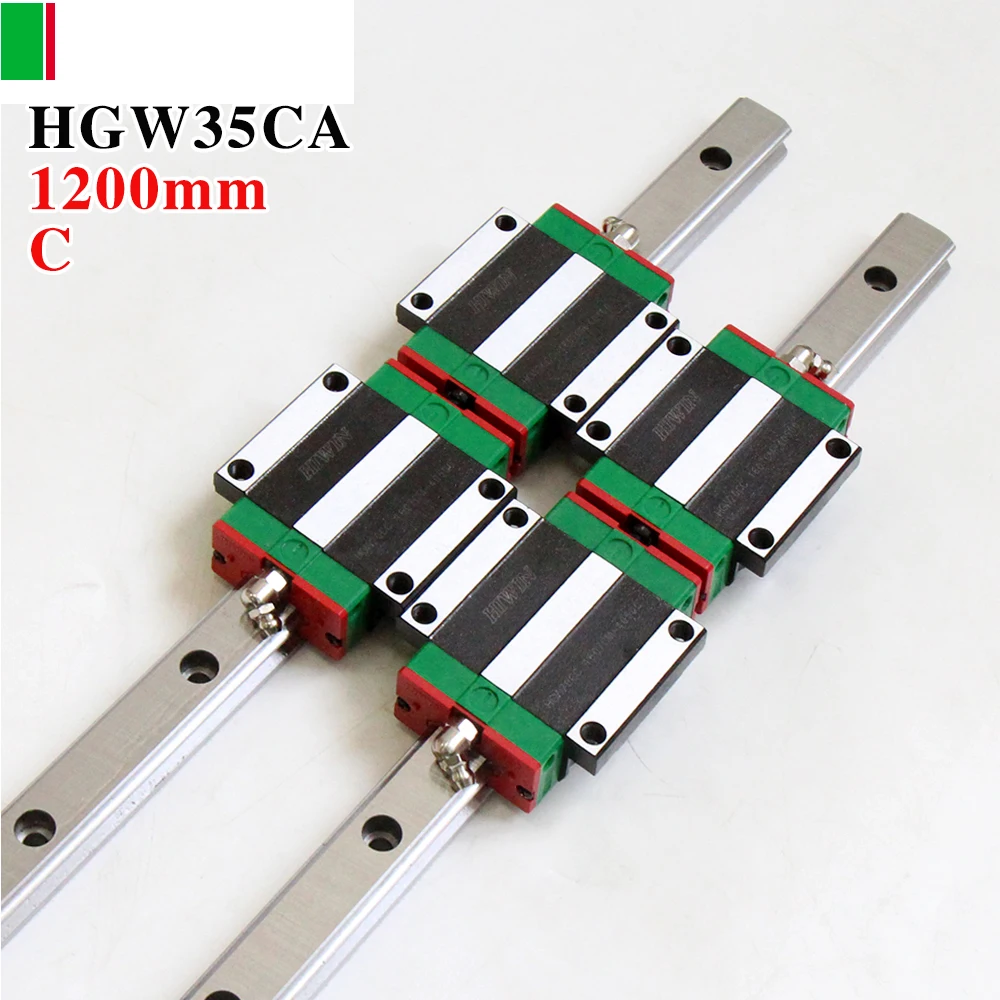
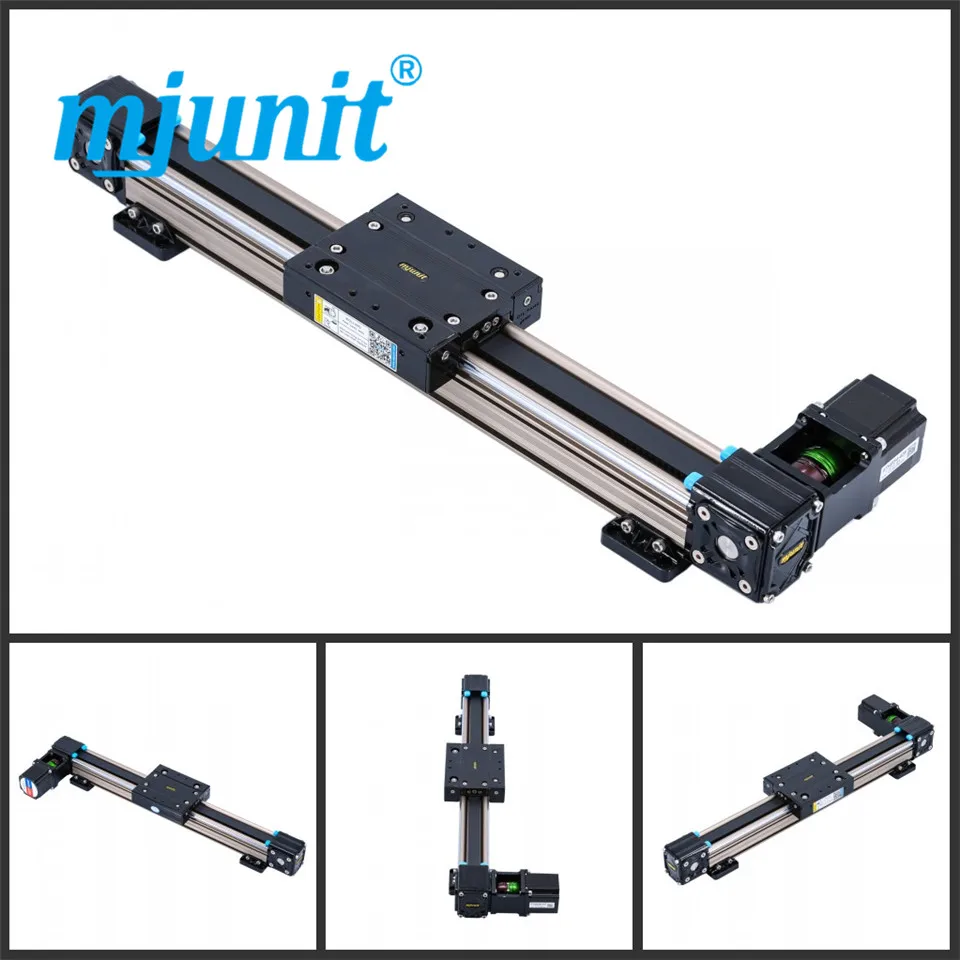
they may not be large (and depending on your tolerances may not be noticeable at first) but once you start driving the table around with the weight of the stock you’re going to mill… then there is the issue of the milling itself… if you’re going to mill light easy to cut materials like plastics etc you may be ok… but as soon as you start trying to cut steel your milled surface is going to move away from the cutter perpendicular to the travel on those rails. You appear to be building a large gantry for cnc milling, but combined side-to-side flex due to using wood instead of steel is going to introduce positioning errors. The main challenge I see here (having worked on CNC mills from a maintenance perspective) is flex… Posted in cnc hacks Tagged cnc, CNC router, linear rail, router Post navigation You can check out ’s demo video after the break. Now, he’s one step closer to his gigantic CNC gantry router. MDF isn’t the most dimensionally stable material, so will be covering the whole thing in a coat of epoxy very soon. The now-supported rail was mounted to a piece of MDF with a few bolts and washers. Yes, we also hate the mix of metric and imperial units in that description, but the results speak for themselves. After drilling a 5/16″ hole every 12 cm, he tapped these holes out to receive 3/8″ threaded rod. He put a 90° notch in a 2×4 to support his 25mm rail, and clamped it down with a piece of plywood. There aren’t many tools needed to build ’s rail. came up with a great way to build his own supported rail so he can build his very large CNC router. For any home tinkerer trying to reproduce these supported rails, the problem of cost comes up very quick these rails can run over $100 for just a few feet. Some of the very largest – and coolest – CNC machines use supported linear rail for their movement axes.
